Football boot design
NDA Project - Removed all relevant information.
Using computational design, I designed a football boot that used a plastic element to control how easily the ball could be stopped and controlled by a player. My algorithm allowed us to CNC mill tooling to generate 7 samples with different parameters. These were tested using a ball cannon that fired footballs at 60 kmph and measured a few metrics. These were plotted using a Taguchi matrix and I could then identify the parameters that were most important and optimize for them.
The final design achieved some really tough targets. To supplement the pitch of this, I created marketing materials showing both really footage of testing, and CGI footage that was used in the internal pitching of the client. Sadly the project was cancelled just before production.



Geometry Design
The key metrics of the geometry were defined based on theories of how the geometry would work.
The Height of the geometry and the with of the arms in 2 dimensions.

Heat Pressing
We discovered that the leather needed to be preshaped so it could fit the layers of foam, glue and RHEON parts. The best way to preform the leather was to first heat press with a two part tool.
The heat press tooling was designed to shape leather. This placed a large number of constraints on the heat press plate.
For example: it needed to be smooth enough to not rip the material. The design, therefore sampled the injection mould tooling.
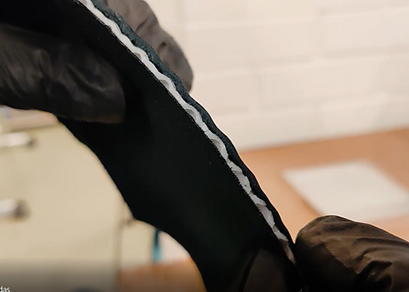




28 Machined Tools
After minimising the total number of tools, 7 sets of tools needed to be made.
2 Heat press tools, 2 Injection moulding tools. Per part.
The grasshopper code I created was designed to make the creation of these simple. It was possible to create all the needed tools in a few hours.
The script took advantage of the manufacturing method meaning there was no need of complex boolean operations, making the tool generation much quicker.
I worked with a colleague to do a tool check. We checked through all the tools, checking for draft angles, minimum measurements, overall dimensions, the meshing of the two parts of the tool.
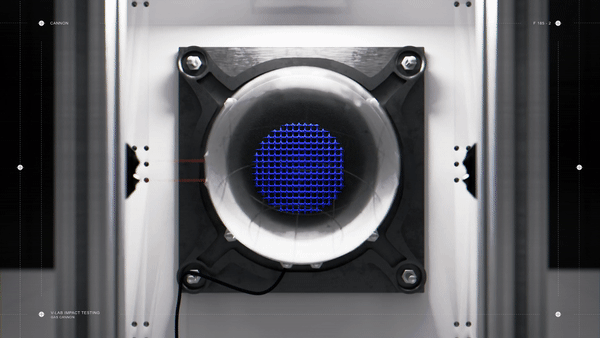
Impact Analysis
The samples were tested using a custom built gas cannon firing footballs at 60kmph.
There were multiple metrics measured to analyse the effect of the part.
We evaluated the impact force, the coefficient of restitution and the heatmap of the impact.
From this we could anaylse the effectiveness of each independent metric.
After that the metrics are optimised for the final part.